welcome to joiner CAREERS
Weld Engineering Jobs
We have contract weld engineering jobs on a project-by-project basis. Providing expertise and support, the welding contractor may work on designing and developing welding processes, troubleshooting welding issues, and ensuring that welding projects are completed efficiently and safely.
As a contract welding engineer, you can work on many different types of welding processes. Additionally, contract work can offer a level of flexibility and freedom that may not be available in a traditional full-time engineering role.
Contract Weld Engineering Jobs
We give self-employed contract welding engineers an incredible platform to showcase their individual talents. A welding engineer may find client projects for all companies, from utilities to manufacturing, contingent on their engineering background knowledge and prior work experience. Many welding engineering professionals are versatile, and understand more than one welding process, and many understand different mechanical joining methods.
Weld Engineering Educational Requirements:
Grow your network with the JOINER Services platform and build a career as a self-employed contract weld engineer.
4-YEAR BACHELOR’S DEGREE
- Welding Engineering Technology
2-YEAR ASSOCIATE DEGREE
PROFESSIONAL CERTIFICATION
- American Welding Society
- Certified Welding Inspector
- Certified Welding Engineer
- Any welding certification from an accredited welding institute
OR +5 YEARS OF INDUSTRY EXPERIENCE
- Welding Technician
Do you meet our weld engineering qualifications?
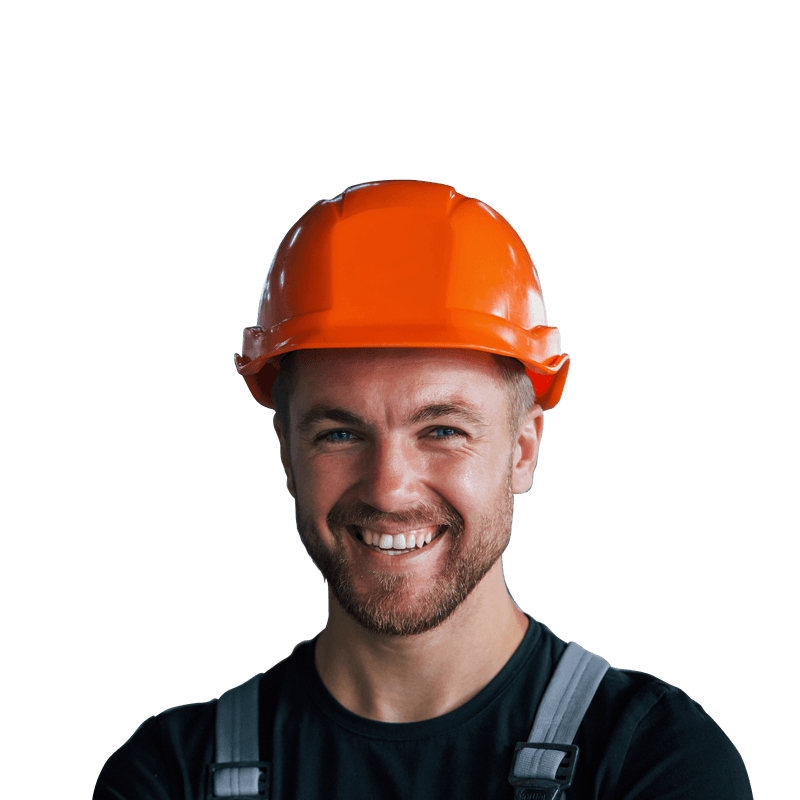
You will have oversight of client’s complex weld engineering projects
Our weld engineers must have some knowledge of the following weld or joining processes:
- Laser Welding (LW)
- Gas Tungsten Arc Welding (GTAW)
- Resistance Spot Welding (RSW)
- Shielded Metal Arc Welding (SMAW)
- Projection Welding (PW)
- Capacitive Discharge Stud Welding (CD)
- Drawn Arc Stud Welding (DAW)
- Gas Metal Arc Welding (GMAW)
- Self Piercing Riveting (SPR)
- Gluing or Sealant
- Flow Drill Screw (FDS)
- Clinching
Depending on the welding engineer’s specific expertise, many projects listed on the platform for contract welding engineer jobs will introduce them to new client facilities throughout the United States. View our open projects on our engineering service platform if you want a contract welding engineer job.
Weld Engineering Career Path:
WELDING SPECIFICATIONS
Welding engineers oversee and design complex welding joints. To meet quality assurance requirements, a welding engineer must know how to read and interpret welding codes and client specifications. In addition, a welding engineer is responsible for writing the welding procedures for any welding process in the manufacturing facility. A contract weld engineer can help a client write welding procedure specifications (WPS), procedure qualification records (PQR), or welding procedure qualification records (WPQR).
FILLER MATERIAL SELECTION
The engineer must know which welding filler materials to use on each application. The welding engineer needs to know the base material, heat treatment, welding position, welding code or specification, and shielding gas used to select the best filler metal for the welding process. Depending on the welding technology used, the thickness of the filler metal is also a critical factor that the weld engineer can help a client determine which is best for an application.
WELDING EQUIPMENT PROGRAMMING
Welding engineers must know how to program weld parameters in the weld controller and adjust the other weld setting in these welding systems. In addition, clients will use different welding equipment. Hence, as a contract weld engineer, it is vital to learn how to adjust the main welding functions and minor welder settings when operating new welding technology for the first time. The benefit of having a contract weld engineer is they have seen multiple types of welding equipment on each welding project, so they are likely to know how to program the client’s equipment.
ROBOT PROGRAMMING OR CONTROLS ENGINEERING EXPERIENCE
Learning other related jobs, such as robot programming or controls engineering, as a welding engineer is essential. Weld engineers work closely with industrial robots, so robot programming is a great skill to learn in the welding industry. In addition, welding engineers often provide technical support for controls engineers, so understanding how programmable logic control (PLC) works on the manufacturing floor is incredibly beneficial to the success of a project.
WELD QUALITY
A welding engineer must validate welds by either destructive testing or non-destructive inspection methods. Working with a certified welding inspector will help with weld quality assurance during the manufacturing process. A welding inspector will validate the welding operations of the manufacturing process.
WELD TRAINING
Contract weld engineers may be asked to train the client’s engineering staff or weld technicians. They may also be asked to teach an organization’s welders; however, it is good to note that only a certified welding engineer or certified welding inspector can qualify welders.
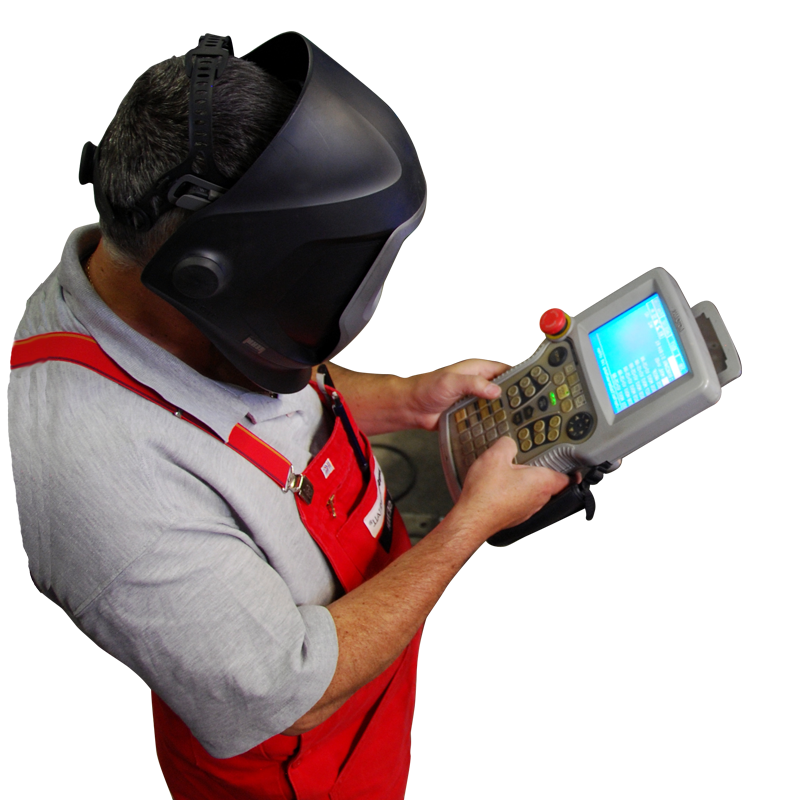
Learn about weld engineering jobs.
Watch this video!
OUR WELD ENGINEER RATES
A welding engineer's hourly rate can vary depending on specific job requirements and experience.
Many weld engineers with robot programming, control engineering, or other joining experience or knowledge will reach annual earnings of well over $100,000.
The rates for welding jobs vary per project and depend on their experience, required technical welding skills, and job location.
A senior welding engineer can earn an above-average salary, especially if they experience unique welding processes or applications.
The current average salary of a welding engineer is around $80,000 a year.
Want to learn more about weld engineering jobs?
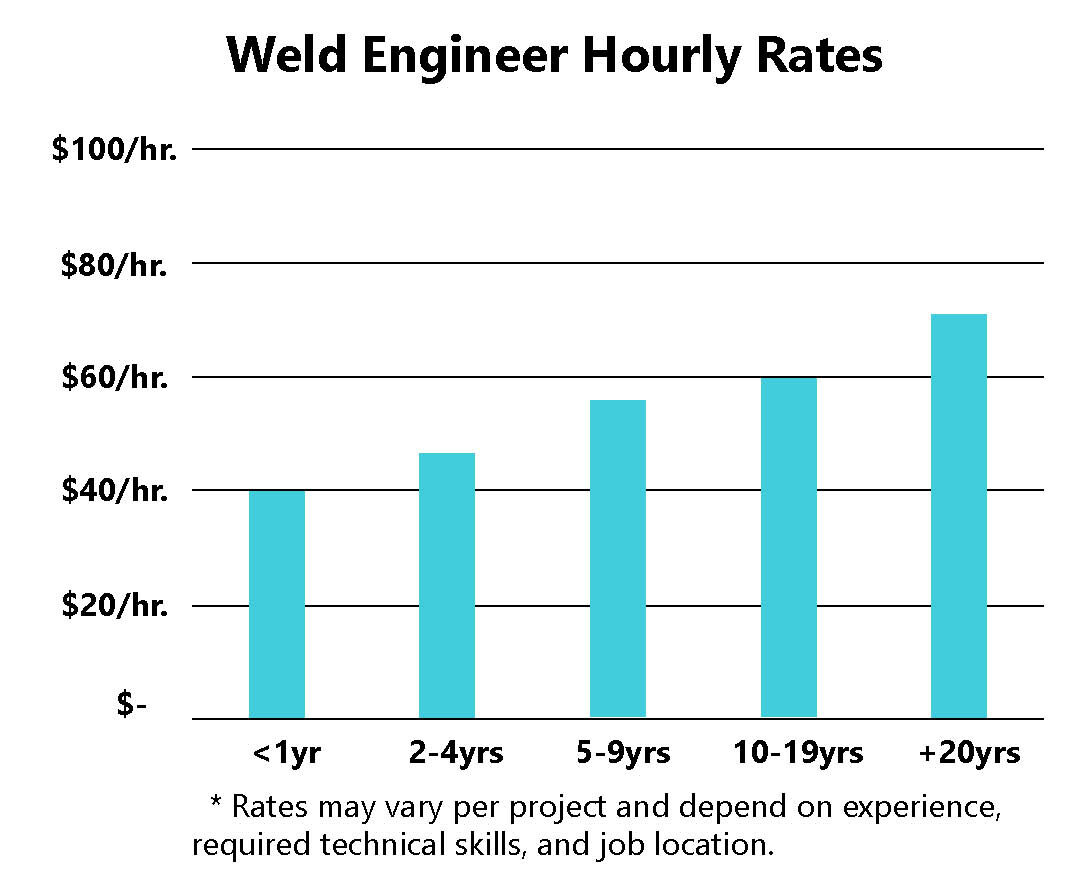
Expectations As A Welding Engineer:
WELD EQUIPMENT
Welding equipment will require maintenance or need replacement of welding consumables. It is also up to the contract welding engineer to repair the client’s welding equipment. Part of a weld engineer’s job description is identifying the right welding equipment for the welding job so the client does not scrap material and uses the most efficient welding process.
PROGRAM WELDING PARAMETERS
The engineer must know how to set and program the client’s equipment welding parameters. They must understand the main welding variables (voltage, amperage, travel speed) and the secondary welding variables such as; torch angle, welding position, shielding gas, welding technique, arc length, and pulsing parameters. Understanding the importance of all these different welding variables is critical to building a successful project.
WELD PROCESSES
Contract weld engineers need to know their client’s welding and joining processes. For example, resistance welding is entirely different from laser or underwater welding. Understanding at least one welding process will help an engineer understand other joining methods. The benefit of using a contract weld engineer is that most have experience in multiple welding methods within the welding industry.
WELD APPLICATION TYPE
During a contractor’s welding career, they will most likely work with different weld applications, from manual welding, semi-automated welding, or fully automated robotic weld systems. Likewise, welding engineer jobs will offer engineers a large variety of experience with different application types, especially contract engineers. As a contractor, each welding engineer’s job description is different, so most will have gained some experience with different types of applications.
WELDING SPECIFICATIONS AND WELD QUALITY
Contract weld engineers must learn the client’s weld specifications and code requirements and ensure all welding processes meet these standards. In addition, the weld engineer’s responsibility is to create welding documentation to meet weld quality standards, like welding procedure specification (WPS) and procedure qualification record (PQR) sheets. Documentation control as a welding engineer is highly critical because of the consequences if the weld fails.
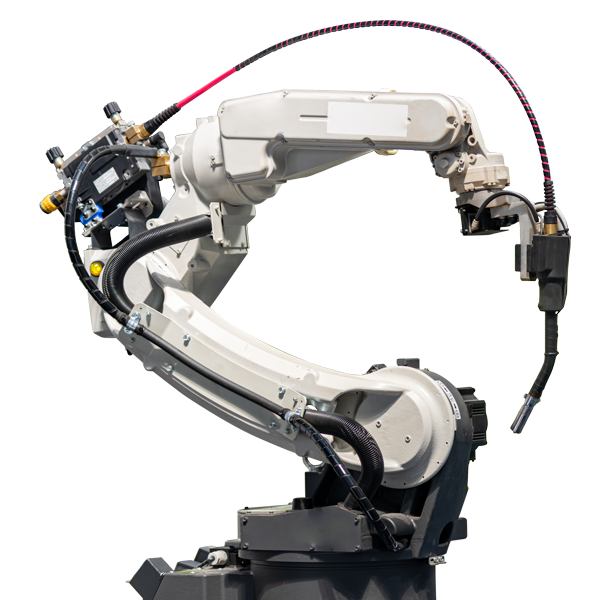